Spur gears are one of the most widely used gears in various industrial applications. They are known for their simplicity, low cost, and efficiency in transmitting power between parallel shafts. Spur gears are available in various sizes and types, and they are manufactured with either involute or cycloidal profiles.
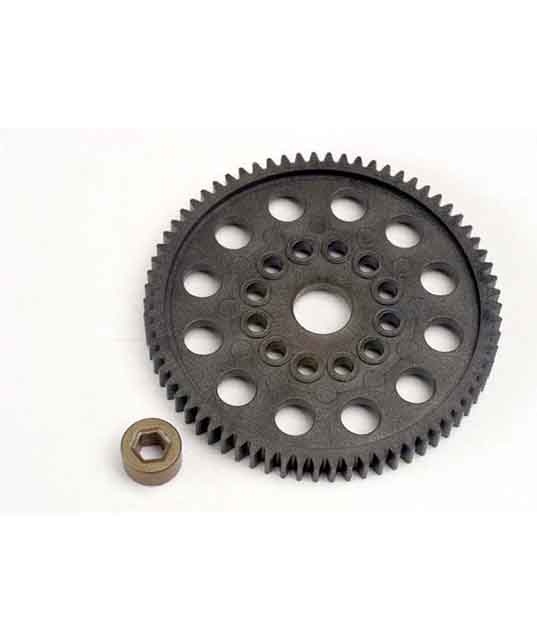
Involutes Profile and Interference:
Involutes profile is the most common profile for manufacturing spur gear teeth. It has 20 pressure angles and provides an efficient contact between the meshing gears. However, involute gears are prone to interference. Interference occurs when two gears are meshed, and the involute portions of the teeth mate with the non-involute portions of the mating gear. This results when the number of teeth on the smaller of the two meshing gears is less than a required minimum. The interference can cause noise, vibration, and damage to the gear teeth.
Undercutting:
To avoid interference, undercutting is used in some manufacturing processes. Undercutting means the removal of material from the base of the gear tooth to create clearance for the mating gear. Though undercutting can prevent interference, it also weakens the tooth at its base. It reduces the contact strength, and under heavy load, the tooth can fail.
Corrected gears:
To solve the problem of interference without undercutting, corrected gears are used. Corrected gears are also known as modified gears. In corrected gears, the cutter rack is shifted upwards or downwards. As a result, the gear tooth profile is altered, and it does not mate with the non-involute portion of the mating gear. This allows full tooth contact and eliminates the possibility of interference.
Importance of Corrected Gears:
Corrected gears have significant advantages over undercut gears. Unlike the undercut gears, the corrected gears have a higher contact strength, better load distribution, and longer service life. Moreover, the manufacturing process for corrected gears is simpler, and it can be done without any manual intervention. The gear teeth produced by the corrected gear method have a higher accuracy and precision than the undercut gears.
Conclusion:
In summary, Spur gears are widely used in various industrial applications. The involutes profile is the most commonly used profile for manufacturing spur gear teeth. However, it is prone to interference. To avoid interference, undercutting is used. Still, it weakens the gear tooth base. Corrected gears are an excellent solution to this problem. They provide full tooth contact, better load distribution, and a longer service life. Therefore, corrected gears are preferred over undercut gears.